Técnica F1Así se hace un monocasco de Fórmula 1
Se trata de la parte más importante del monoplaza, sobre la que descansan las claves del rendimiento del conjunto y la seguridad del piloto. Un equipo especializado emplea seis semanas de trabajo durante 24 horas al día para crear uno de los cuatro monocascos necesarios para completar una temporada.
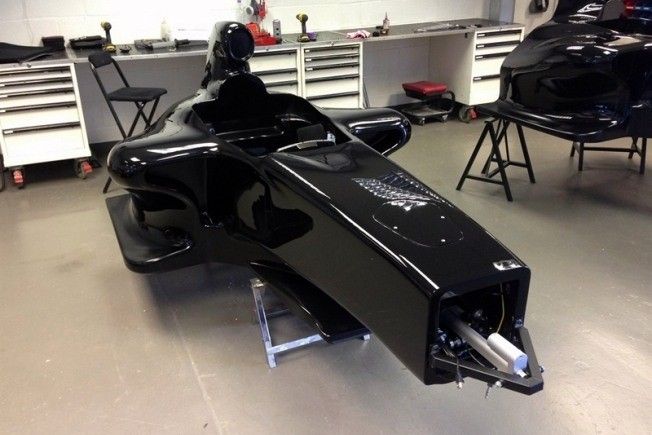
Cuando el monoplaza construido por cada equipo no ha terminado aún la temporada de competición, el siguiente ya ha sido objeto de muchos miles de horas de desarrollo antes de su debut en el mes de febrero del año siguiente. El primer paso en la construcción de cualquier automóvil nuevo es la fabricación del monocasco, la célula de supervivencia de fibra de carbono que alberga al piloto, el tanque de combustible y la batería de recuperación de energía.
Este componente extremadamente complejo y costoso, del que únicamente se construyen cuatro unidades por temporada, es el trabajo más importante del año para el departamento de composites.
Antes de embarcarse en un proyecto tan grande (debido al tamaño del trabajo, el monocasco es el primer componente que se construye), el equipo de entrega del proyecto realiza una reunión de revisión en profundidad para garantizar que está preparado para la tarea que tiene por delante.
Gerry Higgins, jefe de fabricación de McLaren, explica que “aproximadamente un mes antes de comenzar la producción del primer monocasco, recibimos los primeros diseños detallados de la oficina de dibujo y celebramos una reunión de lanzamiento del proyecto. En esa reunión revisamos el programa del año anterior, discutimos lo que aprendimos de ello y lo que no funcionó tan bien como nos hubiera gustado; lo que deberíamos evitar y cómo podemos mejorar”.
Crear un monocasco no es tan simple como añadir meticulosamente capas de fibra de carbono a un molde -aunque eso ocupa la mayor parte del trabajo-, sino también comprender cómo optimizar el montaje, el proceso de laminación, el mecanizado requerido una vez que se haya curado el chasis y la unión detallada necesaria para pegar las piezas y montar un todo.
Los primeros patrones
El primer paso en el proceso es la creación del trabajo de patrones. Se trata de una réplica a tamaño completo de la forma externa y las dimensiones del monocasco, a partir de la cual se creará un molde.
Los mecánicos de patrones pasan dos semanas creando fielmente la forma del automóvil a partir del bloque de montaje, una resina de poliuretano duradera de colores brillantes, a partir de la cual se producen herramientas de moldeo de carbono laminado. Este es un proceso crítico, ya que el trabajo de patrón formará la base para todas los chasis creados, por lo que se requiere una cantidad considerable de tiempo y esfuerzo en el mecanizado, ensamblaje y acabado.
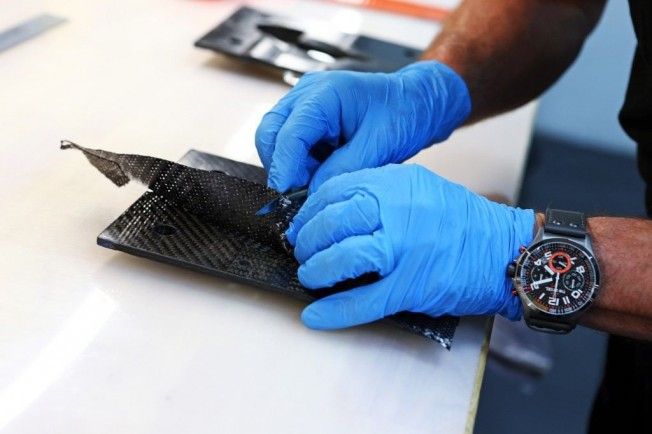
La fibra de carbono debe ser utilizada con suma precisión.
Haciendo el molde
El patrón de trabajo forma la base para el molde de fibra de carbono. En esencia, lo que crea es una imagen negativa del chasis en la que se pueden aplicar las capas finales de fibra de carbono para formar el monocasco.
El molde se parece en cierto modo a una bañera en la que colocaremos fibra de carbono para construir el coche real. Hacer cada molde lleva aproximadamente una semana y media de trabajo.
El paso final: el monocasco
Una vez finalizado el molde, la mayoría del trabajo se lleva a cabo cuando los laminadores comienzan a construir el monocasco. Como los monocascos deben ser increíblemente fuertes y totalmente precisos, los ingenieros utilizan la alineación láser para colocar con precisión cada pieza de fibra de carbono. Los láseres emiten un contorno en el molde, mostrando a los laminadores la alineación exacta de la siguiente disposición.
El monocasco está construido en dos partes, una superior y otra inferior, y es increíblemente compleja. En total, hay unas 600 operaciones de laminación separadas, 30 operaciones de reducción de vacío y 10 ciclos completos de curado en autoclave, todos construidos con seis materiales diferentes de fibra de carbono, ocho materiales de núcleo de nido de abeja diferentes y tres adhesivos distintos.
Un equipo especializado de laminadores trabaja las 24 horas del día, los 7 días de la semana
Un trabajo que una persona tardaría seis meses en completar, se termina en seis semanas con un equipo especializado de laminadores que trabajan las 24 horas del día, los 7 días de la semana. Es decir, el departamento opera a tiempo completo los siete días de la semana, pasando a una tripulación ligeramente reducida sólo durante las noches de los fines de semana. Una vez que se completan las dos mitades, se fijan con una banda laminada adicional que une cada capa superpuesta.
Los toques finales
Tras laminarse el monocasco, éste va al taller de ensamblaje de composites, donde se agregan más detalles. Aún debe ser mecanizado para permitir que los componentes se atornillen o peguen a él: incluyen las estructuras de choque deformables estandarizadas en cada lado, los elementos auxiliares del pontón y una serie de piezas unidas externamente.
Una vez completado, el chasis se entrega al taller de pintura para rociar, antes de llegar finalmente al área de construcción de automóviles de la fábrica, donde se agregarán los sistemas de la unidad propulsora, la suspensión, el sistema hidráulico y la electrónica para convertirlo en un automóvil de pleno funcionamiento.
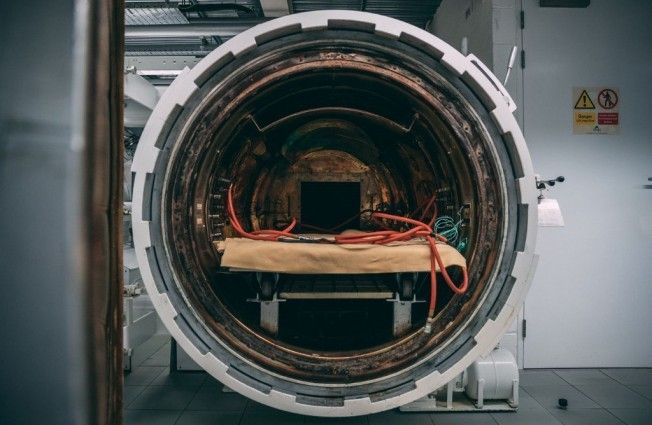
El autoclave es algo similar a un horno en el que se cura el monocasco para unificar las láminas de fibra de carbono y otorgarle sus ventajosas propiedades.
Hay que hacerlo bien
Un trabajo tan enorme y complejo está lleno de dificultades. Y, para Higgins y su equipo, equivocarse simplemente no es una opción, ya que causaría enormes repercusiones prácticas y logísticas a una parte crítica del programa de pretemporada, ya de por sí extremadamente apretado y medido.
“El nivel de complejidad requerido para construir un monocasco generalmente aumenta de un año a otro”, dice Higgins. “Gran parte de eso viene de tratar de perder peso y de aumentar la resistencia. Aprendemos constantemente, hay mucha interacción entre los laminadores y los diseñadores durante ese período de construcción inicial a medida que aprendemos cómo hacer que todo funcione correctamente junto con el molde inicial. Una vez que ha ido de manera correcta en esa fase inicial con el primer monocasco, tenemos la seguridad y la confianza necesarias para comenzar con el segundo”.
Fuente: McLaren Racing
