Bugatti introduce la tecnología de impresión 3D en sus procesos de producción
El fabricante de deportivos afronta una nueva etapa con la impresión 3D. Hasta ahora, solamente había utilizado esta avanzada tecnología en situaciones muy puntuales, pero ahora será una parte fundamental más en la producción de sus modelos deportivos. Bugatti apunta que la impresión 3D ayuda a reducir el peso del conjunto.
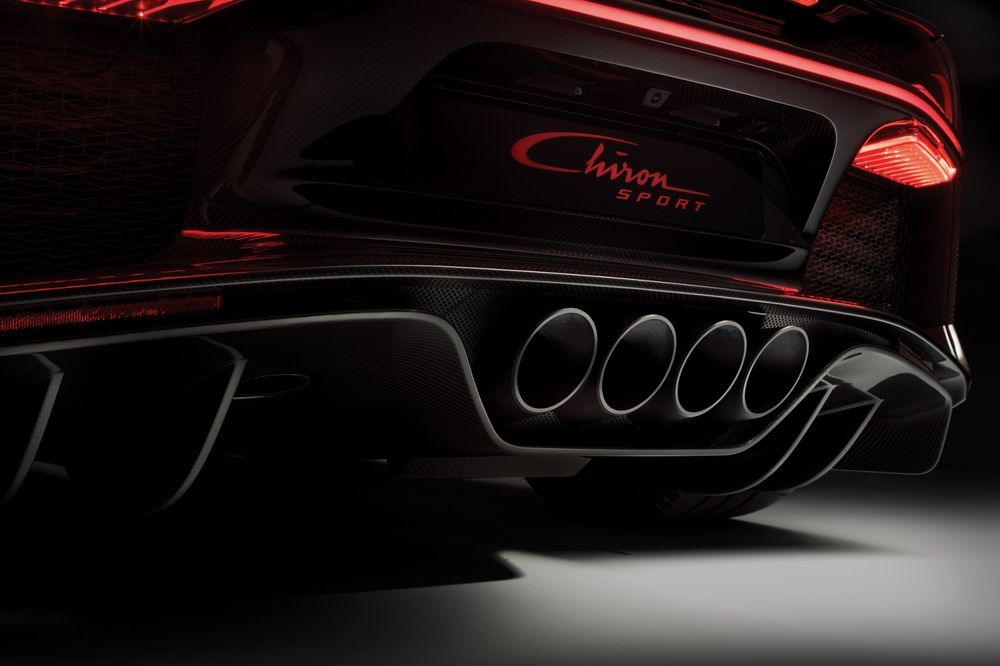
Solamente en ocasiones muy especiales, Bugatti se había atrevido al desarrollo de piezas impresas en 3D. La firma francesa ha aplicado esta tecnología puntualmente, desde 2018, en el Chiron Sport y Divo, además de hacerlo también en los exclusivos "La Voiture Noire" y el Centodieci.
Ahora, la firma anuncia que seguirá utilizando esta técnica como una parte fundamental en el proceso de producción de sus modelos, un solución que ha demostrado una mayor rapidez en la fabricación de componentes de titanio con un acabado preciso y soberbio que cumple con los estándares de calidad impuestos por la marca de Molsheim.
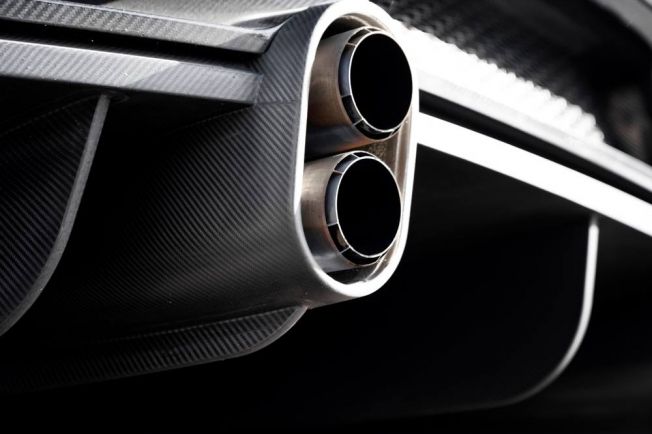
La marca apunta que la impresión en 3D permite avanzar más rápidamente, con un proceso que ofrece un acabado refinado, fino y preciso, con una nivel de estabilidad del material tan sólido y ligero como el acero. Una técnica derivada de la industria aeroespacial aplicada a modelos tan exclusivos los Chiron Pur Sport y Chiron Super Sport 300+.
Una de las piezas que fabrica en titanio es la cubierta del sistema de escape del Chiron Pur Sport, una pieza que comprende también la parrilla y el soporte y solamente pesa 1.850 gramos, nada menos que 1,2 kilogramos menos que la misma pieza equipada en el Chiron, si bien la firma también utiliza otras aleaciones especiales, cuya composición mantiene en secreto.
Esta cubierta tapa los cuatro terminales del sistema de escape, que se aúnan desde seis colectores. Bugatti apunta que el titanio de la tapa contribuye también a ejercer un papel técnico, guiando el calor residual de los gases de escape para que no se acumule calor.
