Bienvenidos al Centro Técnico de Nissan: ingenieros españoles al servicio del mundo
Invitados por Nissan acudimos a visitar su Centro Técnico de Europa en Barcelona, sus siglas son NTCE. Dentro de sus paredes se llevan a cabo un sinfín de operaciones, trabajos y pruebas para que cada Nissan que se compra satisfaga a sus clientes. Trabajo español exportado a todo el mundo.
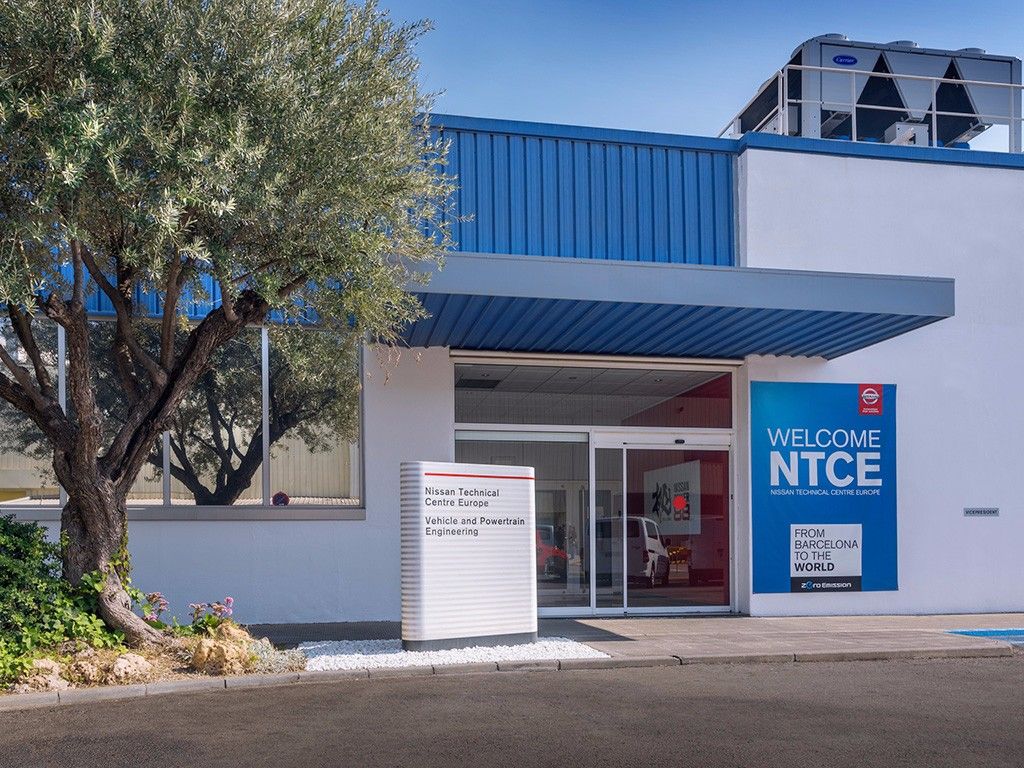
Muchas veces tendemos a menospreciar el trabajo que somos capaces de hacer (hablo refiriéndome a toda España). Pensamos que sí hay detrás algún alemán o algún inglés estaremos en mejores manos, pero centros como el Centro Técnico de Nissan en Barcelona demuestran que tenemos que pensar mejor de nosotros mismos. Aquí un pequeño, pero selecto grupo de ingenieros españoles se encargan de hacer un trabajo vital para la marca japonesa. Acompáñame y te lo demostraré.
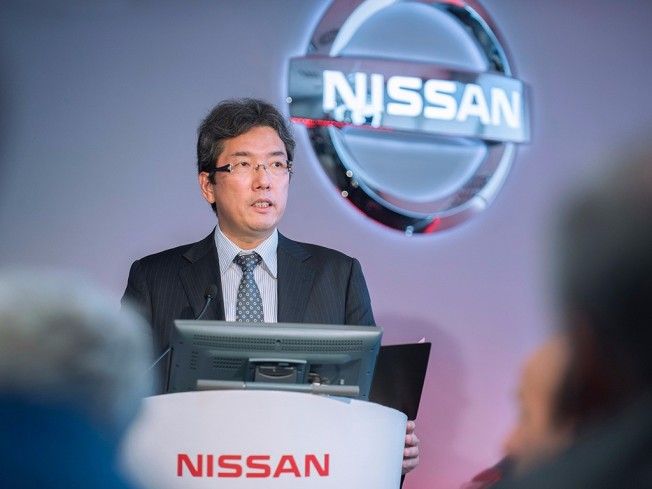
Masaki Toriumi, vicepresidente de I+D en Europa y jefe de estas instalaciones
La zona franca de Barcelona tiene el honor de contar con la planta más grande que Nissan tiene en España. Dentro de sus inmensas instalaciones se encuentran las naves destinadas al desarrollo técnico de vehículos, el NTCE. Una zona muy restringida que guarda grandes secretos, por eso nada más llegar la seguridad del centro nos pone pegatinas por todo el móvil para que así no tengamos la tentación de hacer fotos inapropiadas. Cómo nos conocen estos de Nissan.
Pero antes de adentrarnos en cámaras y salas restringidas es hora de conocer un poco más la historia de este centro, que data de nada más y nada menos que 1968. El Centro de I+D de Motor Ibérica abrió sus puertas ese mismo año, fue el embrión del actual Centro Tecnológico de Nissan Europa en España. Por aquel entonces su trabajo consistía en desarrollar diferentes modelos de camiones de la marca Ebro, tristemente desaparecida. En 1979 Nissan adquirió Motor Ibérica, y fue a partir de entonces cuando el centro se ha encargado de adaptar y desarrollar multitud de modelos, desde el inolvidable Patrol hasta el último modelo en salir de sus líneas, el Pulsar.
Este centro de Barcelona no es el único que la marca japonesa tiene en Europa, sino que son cuatro los que conforman un conglomerado. Sin embargo este, junto con el centro de Cranfield en Gran Bretaña, son los dos pilares más importantes que Nissan tiene en el viejo continente. Los otros dos se encuentran en la ciudad alemana de Bonn y en San Petersburgo, Rusia, donde se realizan las adaptaciones para los mercados de Europa del Este.
El Centro Técnico de Nissan en Barcelona abarca un área de 22.000 metros cuadrados
En conjunto son más de 900 personas las que trabajan en las diferentes instalaciones de I+D de Nissan en Europa, 330 de ellos en Barcelona. Estos se suman a los más de 21.000 empleados que realizan las mismas funciones en diversos países repartidos por todo el globo. Japón, Estados Unidos, India, México, Brasil, Vietnam, Taiwán y Sudáfrica.
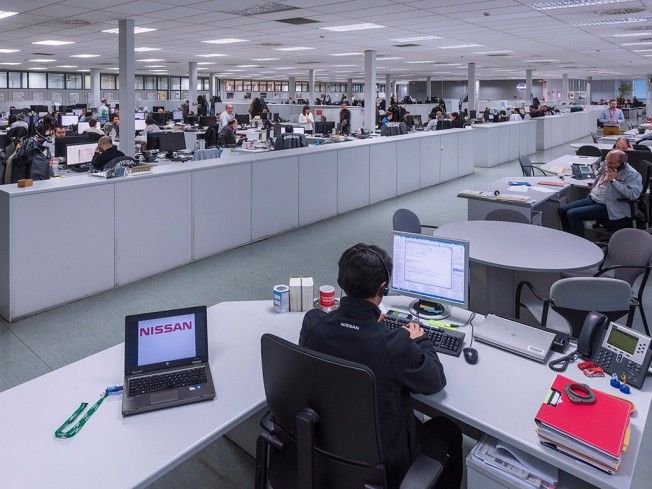
Resulta llamativa la ausencia de paredes, ni siquiera los jefes están encerrados en oficinas propias
Como ya he comentado, el Centro Técnico de Nissan en Barcelona se encarga de realizar funciones realmente importantes para la marca en Europa. En realidad son tres los principales cometidos que tiene asignada la planta: desarrollo de vehículos industriales ligeros, adaptación de todos los motores diésel de Nissan, en todo el mundo, y por último la realización de pruebas de desarrollo de todos los modelos fabricados en las plantas de Europa y Rusia, así como la adaptación de los modelos fabricados fuera y que son vendidos en Europa.
Cómo podrás comprobar son funciones realmente importantes, ya que todas ellas afectan al producto final, más en el caso de los motores diésel. Sí tienes un Nissan diésel, seas de donde seas, su preparación y puesta a punto ha salido de esta fábrica, así de sencillo. El NTCE de Barcelona es el centro de referencia mundial en los motores diésel. Pero vayamos por partes y analicemos que implica cada paso.
Desarrollo de vehículos industriales ligeros
Un lienzo en blanco, o una pantalla de ordenador en blanco, es el punto de partida para el desarrollo de los vehículos industriales ligeros que se lleva a cabo en esta planta. Desde el tornillo más pequeño, hasta la pieza más grande sale de las mesas de diseño de los ingenieros del NTCE. Usando programas avanzados de desarrollo por ordenador, las piezas se moldean una a una. Paso a paso el diseño va creciendo hasta tener un producto previo que se asemejará mucho al final.
Antes de llegar a la fase de producción el prototipo tiene que pasar por una serie de pruebas digitales para ver que todo está en su sitio y para comprobar que no aparecerán problemas futuros por un diseño indebido. Es aquí donde se notan los cambios que ha sufrido el mundo del automovilismo. Hace unas décadas este proceso habría supuesto mucho gasto y muchas más horas de trabajo. Ahora gracias a la digitalización el desarrollo no solo es más rápido y económico, sino que es más eficiente. Según comentan antes se requerían varias decenas de unidades de pruebas previas antes de llegar al producto final, ahora un ordenador nos da el visto bueno antes de empezar a trabajar.
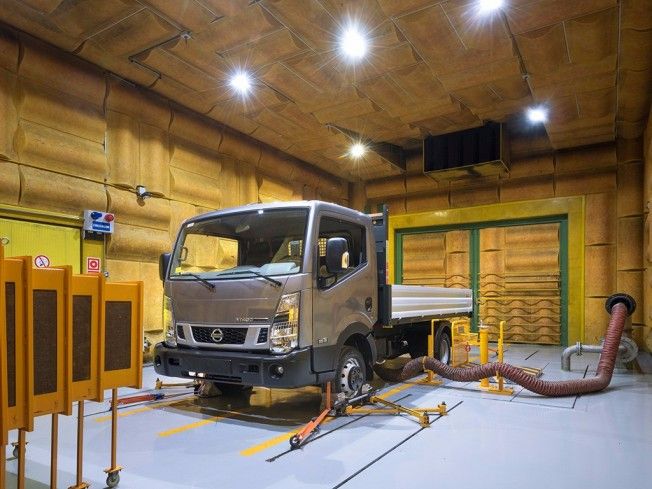
El vehículo industrial NT500 es el modelo más grande que se desarrolla en la planta, aquí lo vemos en la sala semianecoica
En este cometido el NTCE de Barcelona ha liderado diferentes proyectos de desarrollos completos de vehículos industriales ligeros que posteriormente han sido vendidos en Europa y Rusia. Una muestra de ello es el Nissan NT500. También se han encargado de realizar parte del desarrollo físico de otros modelos, como el NT400, el pick-up Navara o la más reciente furgoneta NV200, incluyendo su versión eléctrica, el e-NV200, que se fabrica en las naves aledañas a estas instalaciones.
Adaptación de los motores diésel de la Alianza Nissan-Renault
Si por algo es conocido el NTCE de Barcelona es por su experiencia en motores diésel. De sus bancos de pruebas salen todas las configuraciones que dichos motores tendrán en el mundo entero. Y para ello pasamos de un lienzo en blanco a un bloque en bruto. Los ingenieros españoles reciben de sus colegas franceses y japoneses los motores en su estado más primitivo. Tan solo llega el bloque de cilindros, y son ellos los que tienen que desarrollar y probar todas las piezas complementarias que llevan estos, además de ajustar su funcionamiento a los diferentes estándares de los países en los que van a ser empleados.
Primero hay que empezar por todos los componentes periféricos del motor, cárter, refrigeración, poleas, líneas de combustible, admisión y escape, entre otros muchos componentes. Todos ellos se diseñan en los mismos ordenadores que anteriormente te he mencionado. Una vez se ha completado este paso es hora de fabricarlos para posteriormente instalarlos en los motores. Es aquí cuando pasamos a los bancos de pruebas.
Los ordenadores facilitan la tarea enormemente, cuesta mucho imaginar cómo se hacían estos procesos hace unos años sin contar con ellos
El motor se monta sobre unos carritos con todos los sistemas propios, salvo la caja de cambios que no se asocia a ninguna. A partir de aquí el trabajo consiste en configurar más de 30.000 parámetros diferentes. Un proceso minucioso y muy complicado que afectará al éxito o al fracaso de un coche o una versión del mismo. Vuelvo a repetir que este paso se debe hacer en consonancia con el país donde vaya dirigido el motor en cuestión, no son las mismas especificaciones para Estados Unidos, Europa o cualquier otro lugar del mundo, y ese trabajo se realiza en España.
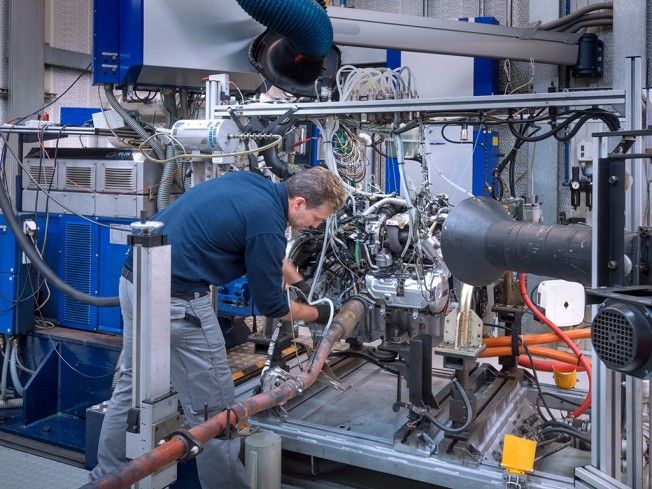
Las pruebas de motores se realizan con todos los componentes instalados, salvo la transmisión
Un total de 17 motores son gestionados desde esta base de operaciones de Nissan, que si le sumamos las posibles variaciones de vehículos, llegamos a las 55 combinaciones posibles. Esto se debe a que aunque un motor sea empleado en varios modelos, eso no significa que tengan la misma configuración, así que hay que adaptarla en función del modelo en el que se vaya a montar, lo que supone un enorme trabajo cros-funcional entre diversos centros técnicos y plantas de montaje de todo el mundo.
Una de las tareas anexas a esta labor es el tema de las emisiones y los consumos. Esto es algo que también se pone a punto en el NTCE y el proceso es una mezcla de última tecnología con el más artesanal de los procedimientos. En este paso del proceso se requiere que el coche esté completamente montado, con todas las especificaciones y todo el equipamiento que va a salir a la carretera. Una vez dispuesto este, se monta sobre unos rodillos que simularán una circulación por carretera abierta, también está presente un enorme ventilador que se encarga de recrear los efectos del viento a diferentes velocidades.
Y es aquí donde aparece el factor humano, porque será un miembro especializado del equipo el que se encargue de conducir el coche. La Unión Europea tiene unos estándares y una reglamentación muy estricta en cuanto a emisiones contaminantes, y obligan a que cada fabricante las cumpla. Para ello se simula una conducción preestablecida en diferentes pasos. El conductor deberá seguir las indicaciones de la pantalla para valorar las emisiones. Haciendo un punto y aparte, estas me recuerdan mucho a la prueba del psicotécnico del carné de conducir, donde había que mantener una bolita dentro de un camino, pero a diferencia de aquella, esta es más fácil de conseguir.
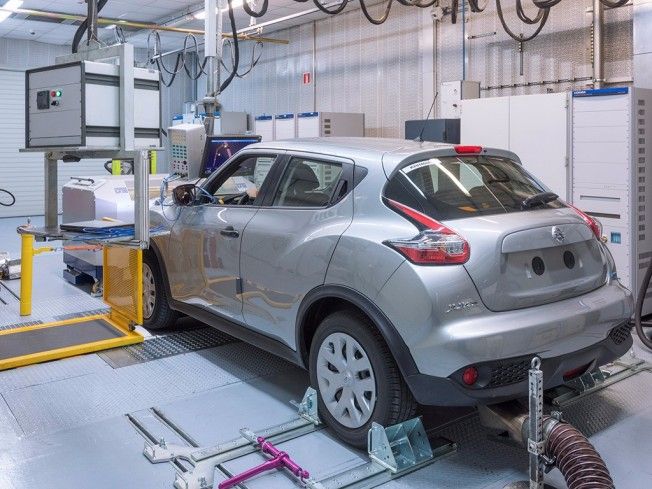
Las normativas europeas deben ser homologadas en estas salas por personal autorizado
Así que desde un bloque en bruto hasta el último paso de homologación, el NTCE se encarga de dar forma a cada motor diésel que montan los Nissan de todo el mundo. Un trabajo muy complicado y oscuro que conlleva una gran responsabilidad y muchas, muchas horas de acierto y error. Resulta curioso como ellos mismos se refieren a este trabajo como tunning, pero la cuestión es que es totalmente cierto.
Pruebas de vehículos y componentes
Por último, y no menos importante, el NTCE se encarga de realizar pruebas de vehículos completos, y de componentes de los mismos. En este ámbito, y además de realizar investigaciones de mercado y análisis de la competencia que permiten definir las necesidades del cliente europeo, se realizan de los ensayos de desarrollo de todos los modelos fabricados en las plantas de Europa y Rusia, de acuerdo a las especificaciones requeridas por los países de destino. Así mismo se realizan los ensayos de adaptación a los requerimientos europeos de los vehículos producidos en otras plantas y comercializados en Europa.
Para cumplir con esta labor los ingenieros de Nissan cuentan con una ingente cantidad de tecnología adaptada para cada ocasión, incluyendo robots de sabe dios que desproporcionado precio. Para que os hagáis una idea, hay una sección que se encarga de abrir y cerrar las puertas del coche. Antes este trabajo lo realizaba una persona, pero desde hace años lo viene haciendo un incansable robot que cuesta la friolera de 3,5 millones de euros, y eso que su papel es bastante sencillo, muy del estilo de los robots que abren y cierran las puertas de los armarios en el Ikea.
La idea es someter a cada coche a una tortura inimaginable, someterlo a unas condiciones que jamás se darían en la vida normal. Hay que llegar al límite de cada pieza para saber que es capaz de soportar. En el NTCE se coge cada pieza del coche y se trata de destruirla de mil maneras, solo si esta cumple con los márgenes de la compañía se utilizará, sino se volverá a diseñar y analizar hasta que lo haga.
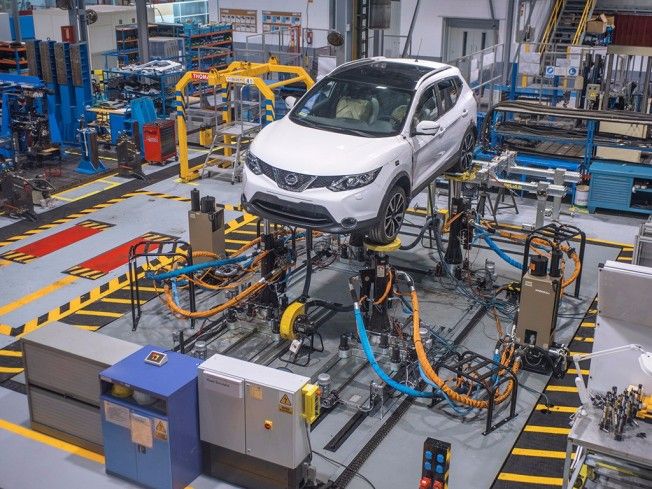
Sorprende el ruido que desprende el coche al ser sometido a este simulador de carretera
Como siempre hay diversas zonas que son más especiales que otras. Así nos encontramos con el departamento del cambio. Un buen tacto del pedal y de la palanca hace mucho en el confort de marcha y por eso los ingenieros se esfuerzan en que cada vez sea más suave. Lo mismo ocurre con las vibraciones o los soniquetes que a veces nos encontramos al emprender la marcha. Expertos en sonido analizan las frecuencias de resonancia de cada material y determinan que piezas deben ser modificadas o eliminadas para que no se produzca el siempre molesto repiqueteo de piezas.
No todo iba a ser trabajo. Nissan deja un espacio a sus trabajadores para que puedan hacer sus experimentos
Para conseguir un trabajo excelente en este aspecto también disponen de una cámara semianecoica. Esta cuenta con rodillos para simular una vez más la conducción, y gracias a todo el equipo se permite medir al detalle la rumorosidad de cada coche, mejorando si fuera necesario el aislamiento de diversas partes del coche para que llegue el menor ruido posible, haciendo los viajes más largos.
Pero sin lugar a dudas las joyas de la corona de la fábrica son el simulador de carretera y las cámaras climáticas. Antes de llegar al simulador un prototipo debe recorrer una serie de kilómetros para comprobar que movimientos son los más perjudiciales y dañinos. Una vez analizados estos se trasladan al ordenador del equipo para que los reproduzca, pero de una forma mucho más exagerada. Este proceso en su tiempo suponía realizar muchos kilómetros durante una media de tres o cuatro meses, gracias a esta máquina el tiempo se ha reducido a tres o cuatro semanas, continuas. Y el coche tiene que pasarla, sino de vuelta a la mesa de diseño. Una verdadera tortura.
Las cámaras climáticas por su parte permiten recrear diferentes ambientes con la intención de comprobar cómo se comportan todos y cada uno de los materiales ante situaciones extremas. Las temperaturas pueden oscilar entre los -40º centígrados hasta los 90º C. Una de las tres cámaras térmicas que disponen cuenta con un banco de rodillos, y es aquí donde empieza realmente la tortura definitiva, porque es aquí donde se pueden simular condiciones realmente insufribles, llegando a recrear más de 50ºC con cuatro ocupantes a bordo y un remolque de 3.500 kilogramos subiendo un puerto de montaña. Situación que como comprenderéis no llegara a darse nunca.
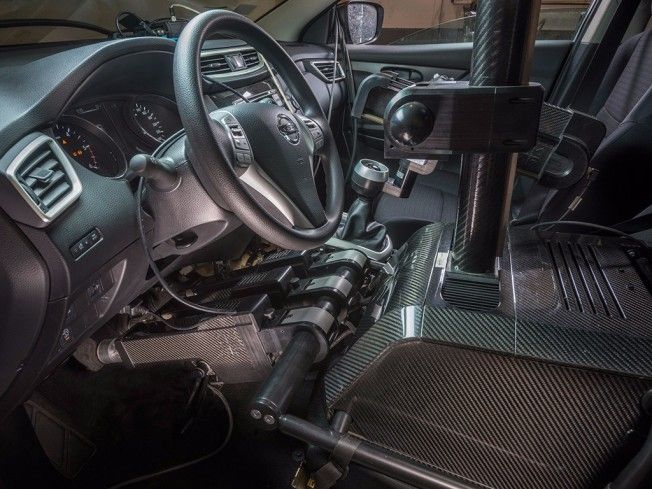
Un robot se encarga de comprobar la resistencia del motor, conduciendo 24 horas al día durante varias jornadas
Por último, ¿te has preguntado alguna vez cuánto tiempo puede aguantar tu motor en marcha? Pues bien, los ingenieros españoles se encargan de comprobarlo. Una sala anexa, especialmente preparada se dedica única y exclusivamente a esta labor. Para no tener que hacer parones innecesarios, se elimina el depósito de combustible de los coches y se instala un sistema de alimentación continua. Puesto que un humano tiene sus limitaciones físicas y fisiológicas, un robot especial, con brazos y piernas, se encarga de conducir. ¿El resultado? Pues bien, el robot, el coche y el rodillo pueden estar dándole que te pego 24 horas al día durante casi una semana.
Este es el Centro Técnico que Nissan tiene en la zona franca de Barcelona. Un pequeño reducto de conocimiento español que se transmite a todo el mundo.
