De la integración vertical al «just in time», y al revés
En el principio, los fabricantes de automóviles recurrían a los proveedores para comprarles piezas que necesitaban para el montaje. En una segunda fase, se trató de aglutinar todos los componentes posibles bajo control directo, pero se acabó volviendo a proveedores. Eso ha quedado en tela de juicio.
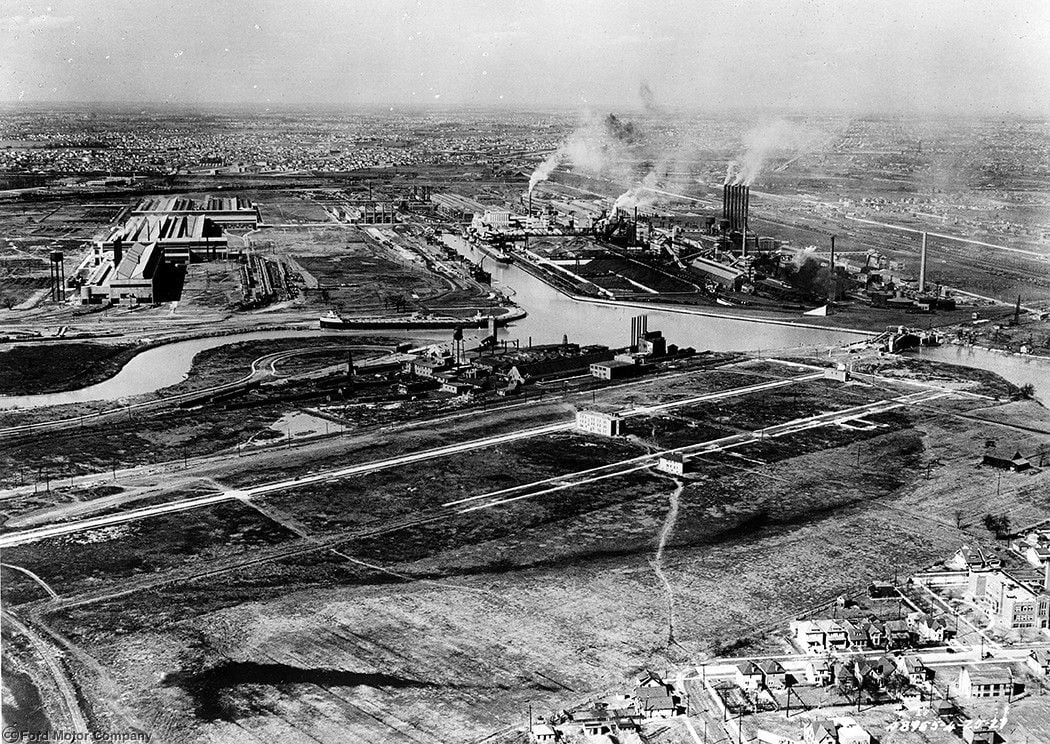
El ejemplo de Ford Motor Company es paradigmático. Cuando se fundó la empresa, en 1903, Henry Ford necesitaba piezas para construir sus automóviles, pero no tenía medios para construirlas todas, de modo que encargó a distintas empresas todo lo que necesitó. Una de esas empresas fue Dodge Brothers.
Durante años, Ford dependió de los hermanos Dodge -que a su vez eran accionistas- para construir sus coches, y el éxito que Ford fue alcanzando sirvió para que John y Horace acabaron siendo ricos. Más adelante Henry retomó el control de su empresa y los Dodge pudieron dedicarse en exclusiva a fabricar sus coches.
En los años 20 Ford logró aglutinar todo lo necesario para fabricar automóviles de forma masiva, en su complejo de River Rouge entraban las materias primas y salían sus coches, prácticamente todo se fabricaba en el mismo complejo, hasta tenía su central eléctrica. Fue un ejemplo de integración vertical casi absoluto. Algunos competidores acabaron haciendo lo mismo, pero no hemos llegado así al presente.
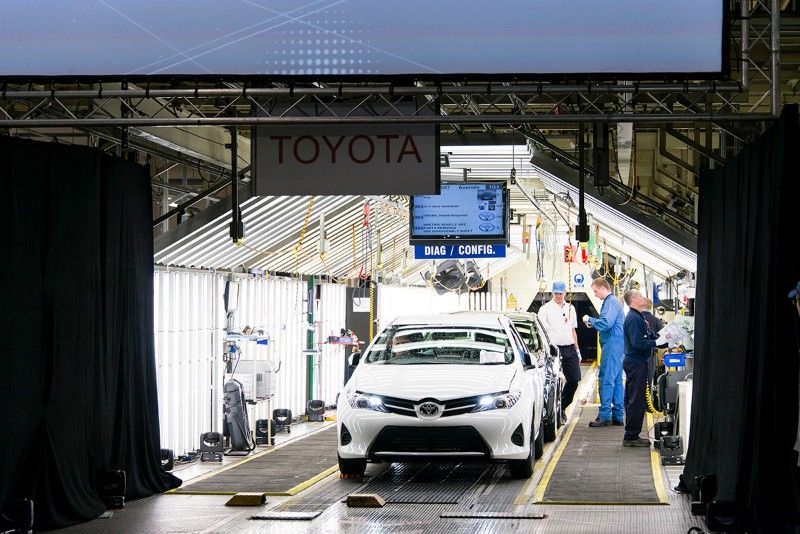
Final de la cadena de montaje del Toyota Auris, el control de calidad visual
Otras ideas se fueron imponiendo, como la de los fabricantes japoneses, principalmente de Toyota. Las distintas piezas se fueron encargando a proveedores con esta filosofía: cada vez que se consume o utiliza una pieza, se pide otra, tratando de minimizar existencias y mantener un flujo fluido de piezas.
De ahí salió el famoso sistema justo a tiempo o «just in time», por el cual los gastos de almacenamiento se reducían a la mínima expresión y se confiaba en que el proveedor cumpliese sus compromisos. Incluso la mismísima Porsche tuvo que apreder esa filosofía y apretar las tuercas de sus proveedores al máximo. También se trató de reducir cualquier desperdicio, el «lean manufacturing», herencia también de Japón.
Antes de «Brexit» vimos algunas interrupciones de piezas provocadas por desastres naturales, como el tsunami y terremoto de marzo de 2011 en Japón
Pero a partir de la crisis del COVID eso ha quedado en entredicho, y como ensayo general podemos citar el «Brexit». La interrupción de la cadena logística provocada por los atascos en aduanas hizo que el suministro de piezas fuese intermitente, siendo necesario para los fabricantes en el Reino Unido almacenar más, o recurrir a medios más costososo de transporte, como el avión. Todo eso incrementó los costes.
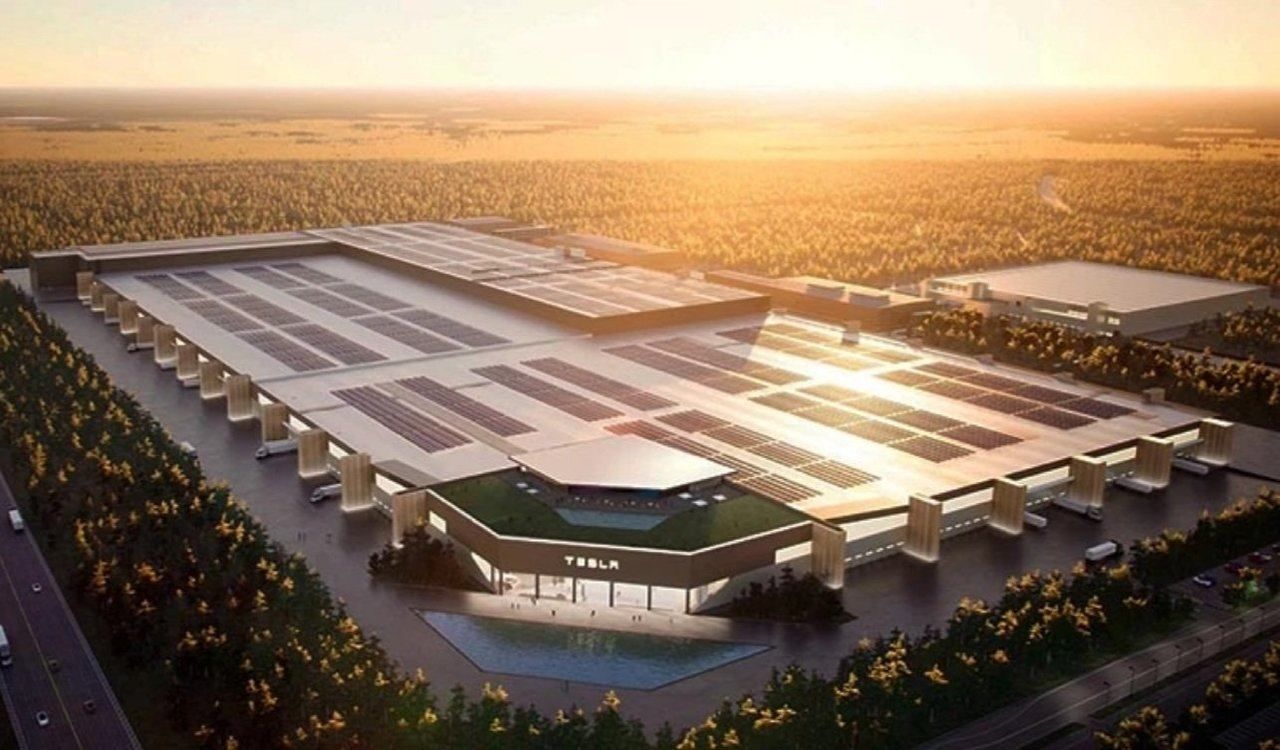
Tesla es un fabricante con un elevado nivel de integración vertical y menos dependiente de sus proveedores
Han pasado varias cosas desde la pandemia, desde el encierro de poblaciones enteras y la interrupción industrial completa de todo lo que no fuese imprescindible, a interrupciones parciales por brotes del patógeno, cierres de fronteras, atascos en cadena logística... y más adelante interrupciones por doquier desde las mismas materias primas. Además, estas se han encarecido.
Esto ha llevado a la parada de las fábricas de montaje, lo cual acaba siendo carísimo para los fabricantes, llegando a la conclusión de que externalizar ciertas piezas no era la mejor de las ideas, aunque sonaba atractivo para todo aquello que tuviese poco valor añadido o que no fuesen capaces de hacer bien, rápido y barato (p.ej., neumáticos).
Las baterías, los microchips o las complejas cadenas cinemáticas eléctricas -no solo son piezas móviles- entran en la lista de lo que los fabricantes no siempre hacen en casa, y que se han replanteado controlar más. Se puede tomar participación empresarial en los proveedores, o absorberlos, o atarlos más en corto.
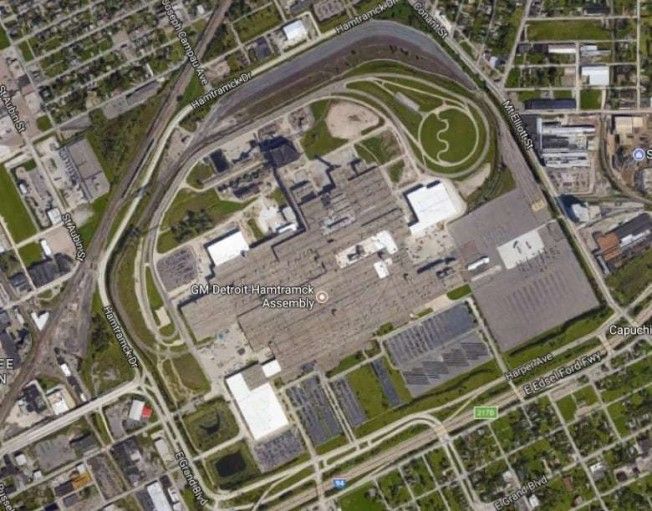
El complejo de fabricación de Hamtramck empezó siendo de Dodge y acabó siendo de General Motors. Tenía hasta su propia pista de pruebas
Aunque difícilmente volveremos a los niveles de integración vertical del pasado, desde las materias primas hasta los vehículos terminados, sí vamos a ver cómo los fabricanes toman el control de todo lo que pueden. Desde luego en cuestión de baterías y componenes de vehículos eléctricos vemos muchos esfuerzos de integración o alianzas en corto con proveedores.
Además, se está buscando una mayor cercanía geográfica entre los proveedores y las fábricas, para reducir lo posible los problemas asociados al transporte, no solo porque los fletes se han encarecido, también por tiempos, por reducir la huella de carbono, o simplemente para tener la situación más controlada en general.
¿Y qué sistema es el mejor? Buena pregunta. Podríamos decir que implique más rapidez, menores costes, más fiabilidad y la misma calidad. La integración vertical total no siempre es lo mejor, de la misma forma que externalizar todo el proceso productivo no lo es, solo fabricantes pequeños recurren a eso, y poco valor añadido se aporta así.
