Fábricas de automoción por todo el mundo se están quedando sin microchips
Cada vez más fabricantes se enfrentan a un problema: no pueden completar más vehículos porque les faltan microchips. El impacto en la producción va a ser de cientos de miles de unidades y aumentará semanas los tiempos de entrega a clientes.
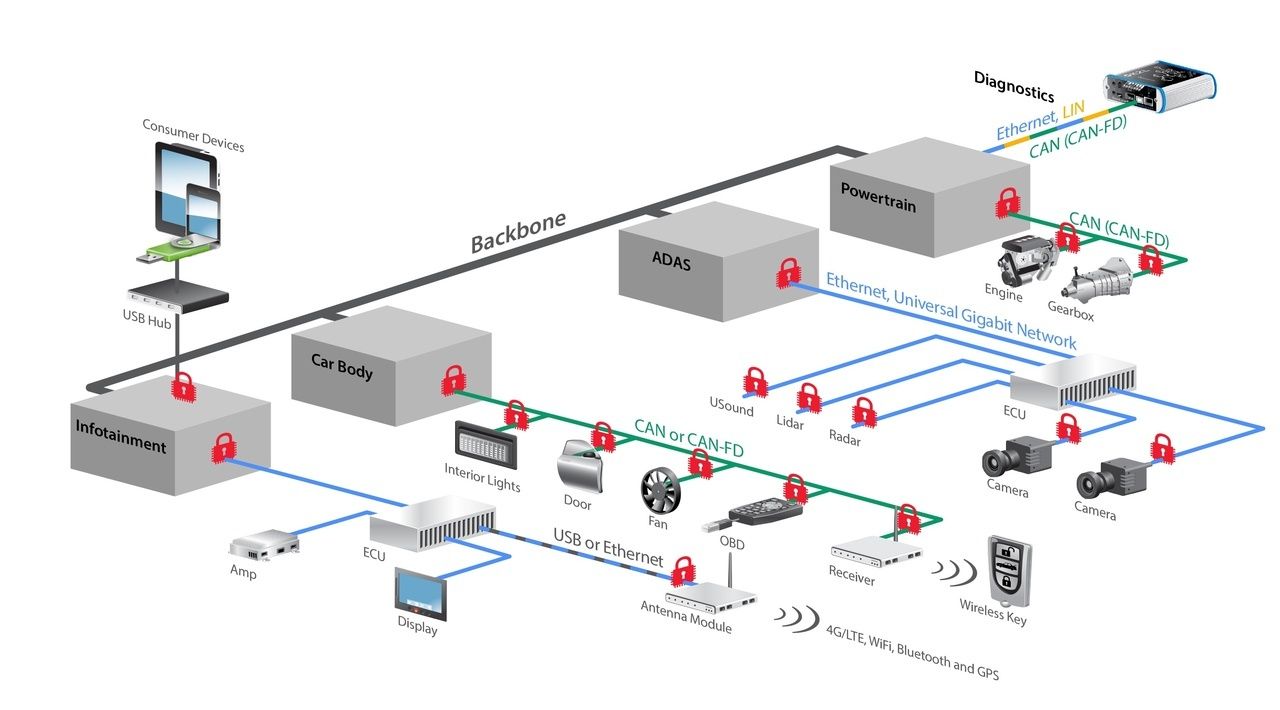
En los primeros coletazos de la crisis del coronavirus, a inicios de 2020, hubo fabricantes que tuvieron que parar fábricas temporalmente porque los proveedores asiáticos ralentizaron o interrumpieron su producción. Sanitariamente no había apenas preocupación por estos lares, pero sí industrialmente. Faltaban piezas. Está volviendo a pasar, pero es más grave.
Una creciente lista de fabricantes están planificando paradas totales o parciales de sus centros de producción para reducir el impacto de la falta de componentes. Hoy día los microchips son fundamentales para diversos sistemas vitales, como la gestión de los motores, sistemas de seguridad (incluso ABS/ESP) o de infoentretenimiento.
Las existencias de microchips están afectando tanto a los fabricantes como a sus proveedores, empresas como Bosch, Continental o Infineon. La magnitud del problema se maximiza cuando un componente viene de un único proveedor y este no puede cumplir con lo pactado. ¿Cómo hemos llegado a esta situación?
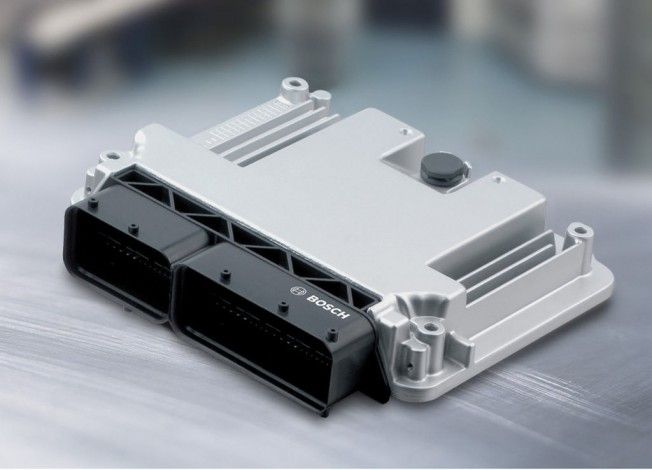
Componentes como las centralitas electrónicas ya son tan importantes como los asientos o las ruedas: sin ellos no se pueden terminar los coches
Volvamos a marzo de 2020
Después de paralizarse la producción en algunos países de Asia, especialmente en China y la provincie de Hubei, empezaron a llegar los confinamientos duros en Europa y Norteamérica, llevando la industria del automóvil al ralentí por no ser esencial. La producción se desplomó.
Obviamente, también se interrumpió el flujo de materias primas y componentes para las fábricas durante semanas. Pero mientras parte de la vida industrial quedaba paralizada, otra tenía que hacer frente a nuevas necesidades que estaban surgiendo. Cientos de millones de personas estaban encerradas en casa, con todo lo que eso implica.
Mientras Occidente se paralizaba, Oriente recuperaba cierta normalidad y actividad industrial
Los fabricantes de microchips recibieron un aluvión de pedidos de empresas dedicadas a producir ordenadores portátiles, consolas, tabletas y teléfonos móviles. Se habían vuelto imprescindibles para trabajar en casa, estudiar, socializar y, en general, matar el rato. Los fabricantes automovilísticos pasaron a un segundo plano como clientes.
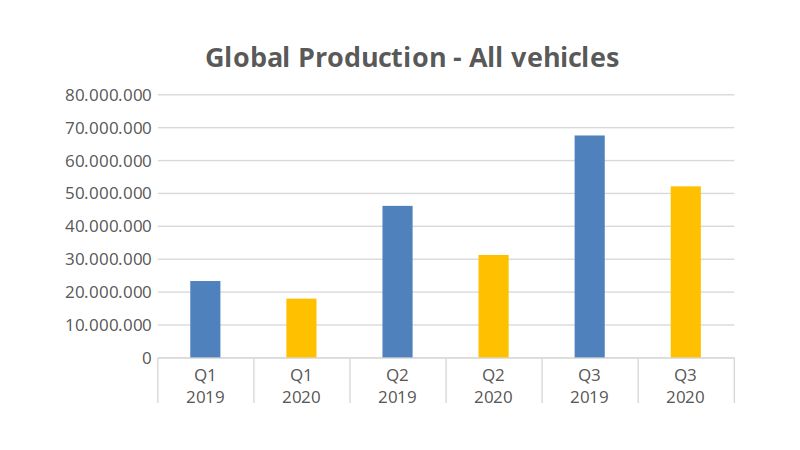
Producción global de automóviles en los tres primeros trimestres de 2020 - Fuente: OICA
Según se fueron aflojando las restricciones en los países productores, la actividad industrial automotriz volvió poco a poco a cierto nivel de normalidad. La demanda había caído en picado y no tenía sentido fabricar a toda máquina. Por lo tanto, la industria del motor siguió teniendo una demanda de bajo perfil de este tipo de componentes.
Más adelante algunos fabricantes pudieron volver a un ritmo de producción más acelerado. Tanto, que los fabricantes de microchips empezaron a ver que les iba a pillar el toro, no esperaban una recuperación de este sector y habían comprometido su producción en la electrónica de consumo. Lo que viene a continuación es fácil de adivinar.
Esta vez la interrupción logística no ha sido por un tsunami, ni un accidente nuclear, ni un terremoto, ni una guerra... simplemente la pandemia más grave en 100 años
Si nos fijamos en 2019, cuando se produjeron a nivel mundial 92 millones de automóviles, el sector automovilístico se llevó una cuota mundial del 10% de los microchips fabricados, especialmente en Taiwán. Además, hay que tener en cuenta que las políticas comerciales de Trump han dificultado las cosas entre China y Estados. El año pasado se produjeron 78 millones.

El oro negro tiene una segunda acepción...
Hay una minoría de fabricantes a los que este problema apenas les está afectando porque disponen de existencias -como JaguarLand Rover o Volvo- y su ritmo de producción no se ha recuperado, pero a la mayoría sí les afecta, sobre todo a los más grandes: Volkswagen, Toyota, General Motors, Stellantis, RenaultNissanMitsubishi...
Ante la escasez de estos valiosos componentes, la producción se está controlando día por día, centrando esfuerzos en aquellos modelos que son más rentables y que sale más a cuenta fabricar antes. Una vez más, la magia del sistema «just in time» se ha ido al garete al haber interrupciones logísticas prolongadas. Las soluciones al problema no son fáciles ni rápidas.
Los fabricantes japoneses, americanos, europeos... son fuertemente dependientes de China, Taiwán... para cierto tipo de componentes, donde se tienen los recursos naturales, las fábricas, el saber-hacer... Llevaría meses o años relocalizar producción para ser «inmunes» a este tipo de problemas. De aquí al tercer trimestre se puede perder una producción entre 600.000 y 900.000 unidades de un total estimado de unos 85 millones -calcula Bosch-.
