La crisis de los mazos de cables es una oportunidad para mejorar diseños de coches
A raíz de la invasión de Ucrania se ha revelado una vulnerabilidad de la industria del automóvil en Europa: sin un componente de bajo coste no se puede hacer un coche moderno. Los mazos de cables se han estado realizando a mano.

Hasta el 22 de febrero, Ucrania era un país relativamente interesante para la industria de componentes de automóviles. Es un país cercano a la Unión Europea, su mano de obra es económica y dispone de los recursos para la fabricación de mazos de cables. Pusimos el ejemplo de Leoni, pero hay más empresas en este sector.
Pero cuando los tanques de Putin entraron en el país la producción se tuvo que interrumpir por la seguridad de los trabajadores. Pasados unos días, ante el temor de perder definitivamente los empleos, la plantilla de Leoni pidió volver al trabajo con medidas extra de seguridad, y así han salido adelante. La producción se ha restablecido a la normalidad puntualmente.
Mientras tanto se han tomado medidas a corto plazo, como recolocar empleados en otras fábricas o derivar la producción a lugares ajenos al conflicto. Sin embargo, entre bambalinas se está cocinando otro cambio, el de dejar de depender de la mano de obra para realizar componentes que tienen un coste bajo.
En este vídeo anterior a la guerra podemos ver cómo se fabrican estos componentes
Básicamente, los mazos de cables se componen de cobre y plástico, habiendo distintos grosores, según la intensidad de corriente que mueva cada cable, y conectores estándar que se llevan fabricando a mano desde hace mucho tiempo. No era algo fácil de automatizar, pero los fabricantes están viendo cómo evolucionar.
Los coches eléctricos necesitarán menos cableado para funcionar que un modelo de combustión interna, lo cual es una oportunidad para automatizar la producción de los cables y que se dependa menos de la mano de obra, ya al margen de que haya más conflictos bélicos donde están los proveedores.
Dicho de otra forma, se va a hacer más por una cuestión de eficiencia y ahorro de costes que por evitar que caigan bombas en una fábrica. Ese riesgo, en realidad, es muy bajo. Importa más lo de automatizar la producción de cables y no solo eso, optimizar el diseño para que sean necesarios menos cables.
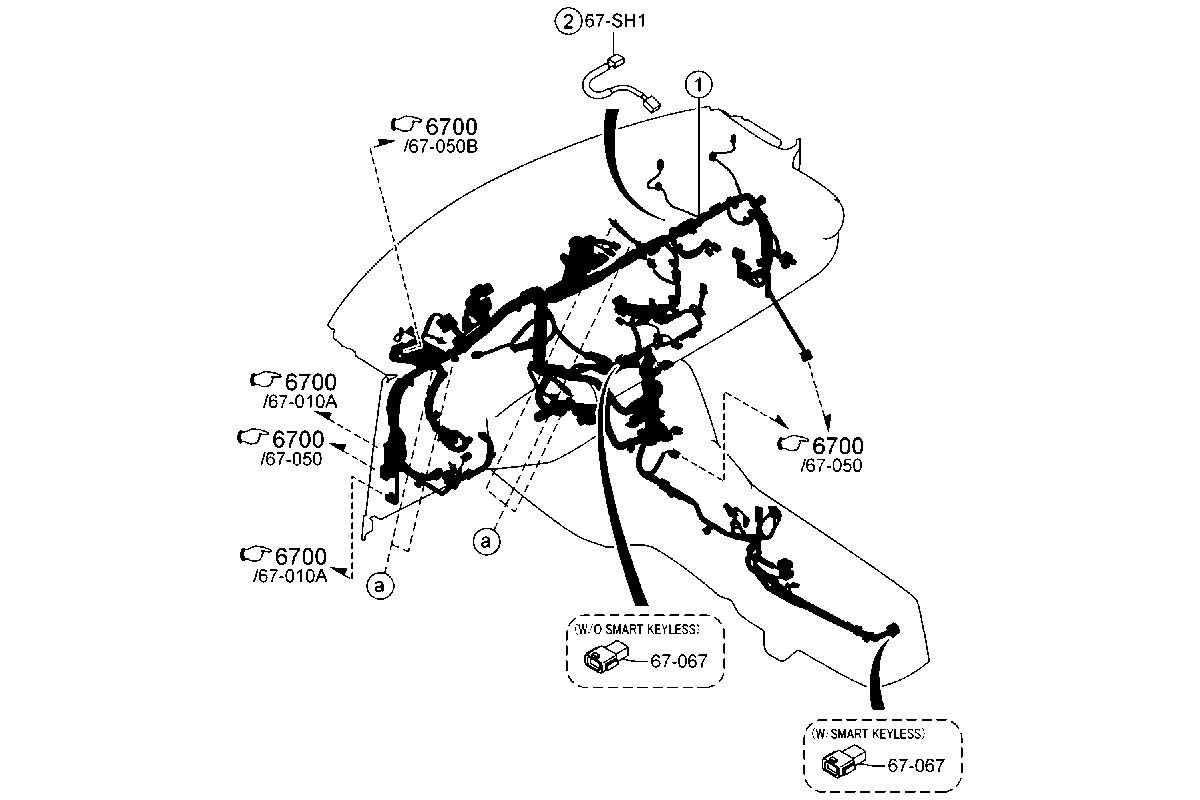
Cableado de interior del Mazda2 de tercera generación (DJ)
¿Os acordáis del Mazda2? Este coche se diseñó con una mentalidad que se definió como la «estrategia del gramo», en la que se buscó rebajar el peso incluso en el cableado. Tesla ahora mismo está entre los fabricantes a seguir en lo relativo a aligerar el contenido en cableado y conexiones eléctricas.
Por ejemplo, una medida elemental de reducción de cableado pasa por reducir los botones físicos, sustituyendo cableado «analógico» por uno totalmente digitalizado en forma de electrónica. Suprimir ciertos equipamientos también consigue el mismo efecto. En otras palabras, se trata de racionalizar.
En los coches eléctricos, dado su peso más elevado que la media, cada kilogramo que se pueda evitar implica alargar la autonomía. Esto es válido para cualquier coche, pero ya se sabe, las baterías almacenan comparativamente poca energía respecto a un depósito de combustible, todo ahorro es importante -aún más-.
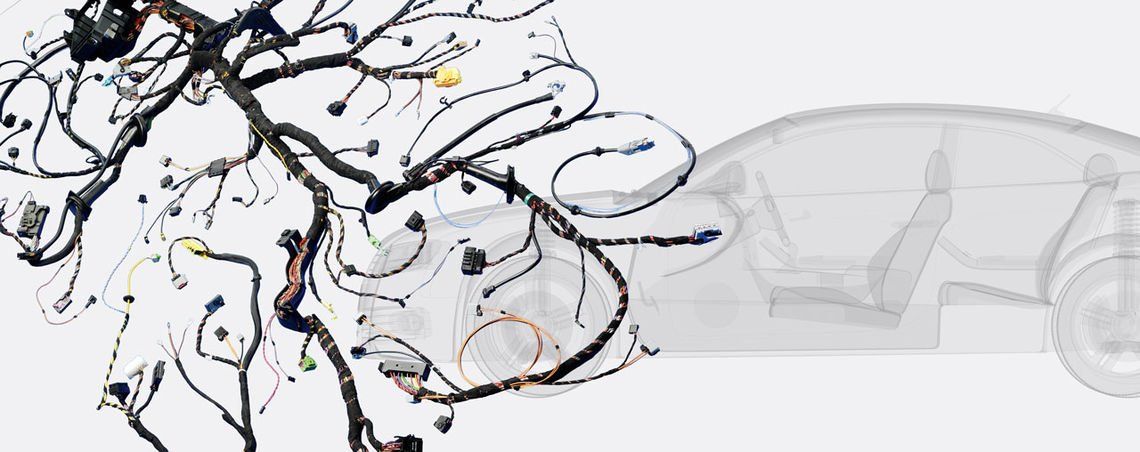
Mazos de cables producidos por Leoni
El diseño de los coches no para de evolucionar y hay margen para optimizar en estos componentes. Por otra parte, simplificando los diseños resulta más fácil automatizar y digitalizar la producción. De hecho, cambiar la producción de cableado de un modelo a otro se puede hacer mucho más rápido a partir de diseños digitalizados.
Todavía la mano de obra de países en vías de desarrollo o con rentas bajas son atractivos para fabricar estos componentes, hasta que se pueda automatizar su producción y sea aún más barato, pero sobre todo, más rápido. De cada crisis de la logística se aprende algo nuevo: terremoto de Japón en 2011, cierres COVID de 2020, accidentes como el de Renesas, etc.
Llevará unos años pegar el salto desde el cableado con mano de obra hasta su automatización total, y cuando eso haya sucedido, la cadena logística tendrá un eslabón débil menos. Estos cambios los empezaremos a ver en generaciones totalmente nuevas, diseñadas ya a partir de este año.
