¿Cómo se fabrica un coche? Visitamos la Fábrica de Renault en Valladolid para contártelo con detalle
Hemos tenido ocasión de pasar unas horas en los diferentes departamentos y talleres de la Fábrica de Valladolid para conocer paso a paso cómo se produce un Renault desde las materias primas al producto final.
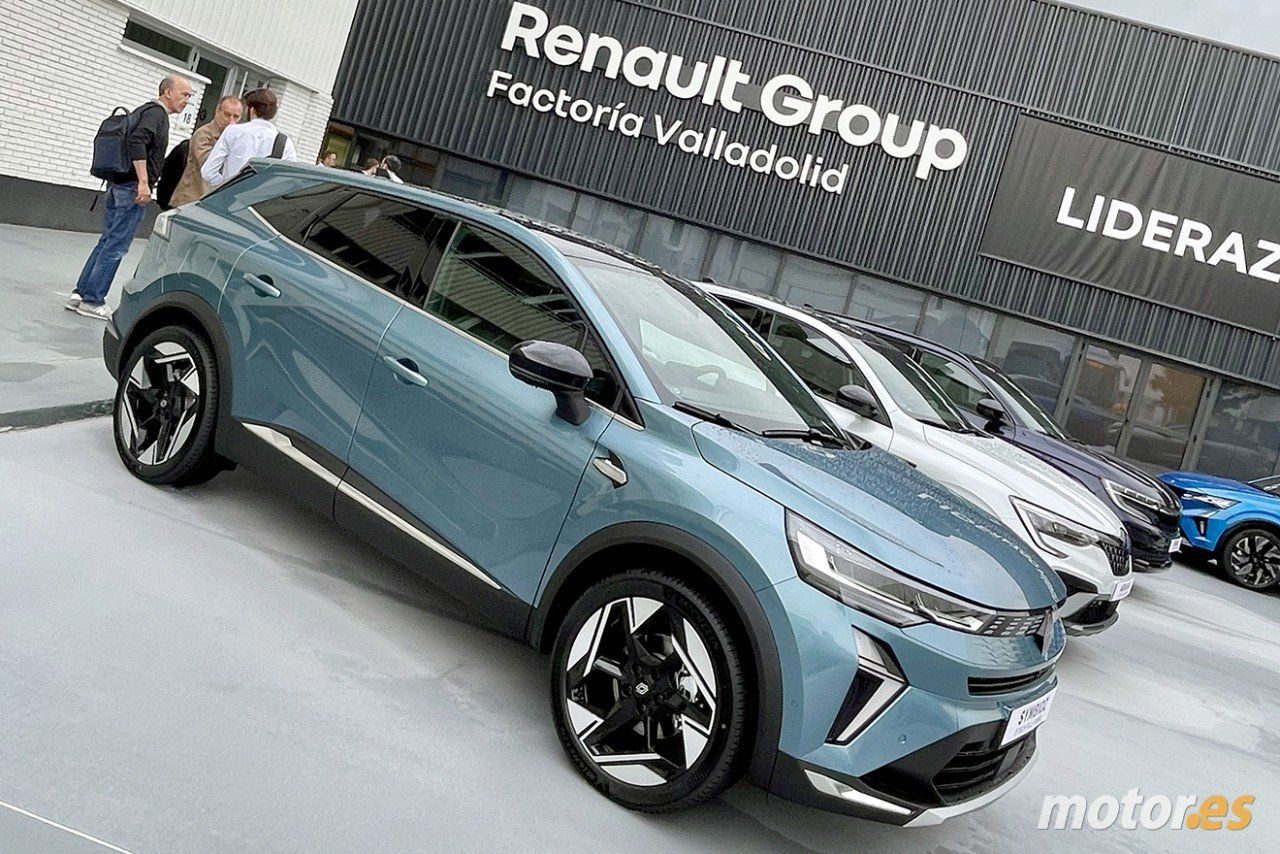
La Fábrica de Valladolid es una de las instalaciones más punteras de Europa. Aquí se fabrican el nuevo Renault Symbioz además del recientemente actualizado Renault Captur y su gemelo el Mitsubishi ASX. La fabricación del Captur y Symbioz completan el despliegue del Plan Industrial Renaulution en España 2020-2024 donde se adjudicaban de cinco nuevos vehículos híbridos a las fábricas de nuestro país. Los otros tres son el Austral, el Espace y el Rafale que se hacen en la Factoría de Palencia.
De esta manera el polo de hibridación de Renault Group está en Castilla y León ya que cinco de los siete coches híbridos que están presentes en su gama se fabrican en España. La llegada de todos estos modelos no solo ha supuesto un impulso al empleo y a la economía sino que también ha permitido a las factorías españolas subir escalones en innovación, digitalización y descarbonización. Por poner solo un ejemplo, en los últimos dos años se ha conseguido una reducción del 42% del consumo de energía y una reducción del 39% del consumo de agua.
Un paso más en la incesante evolución de la factoría vallisoletana que inició su andadura en 1952 de la mano de FASA fabricando el Renault 4CV. Desde entonces, la marca del rombo ha fabricado más de ocho millones de unidades en esta fábrica que he podido explorar en una exclusiva visita guiada por los principales responsables de cada departamento.
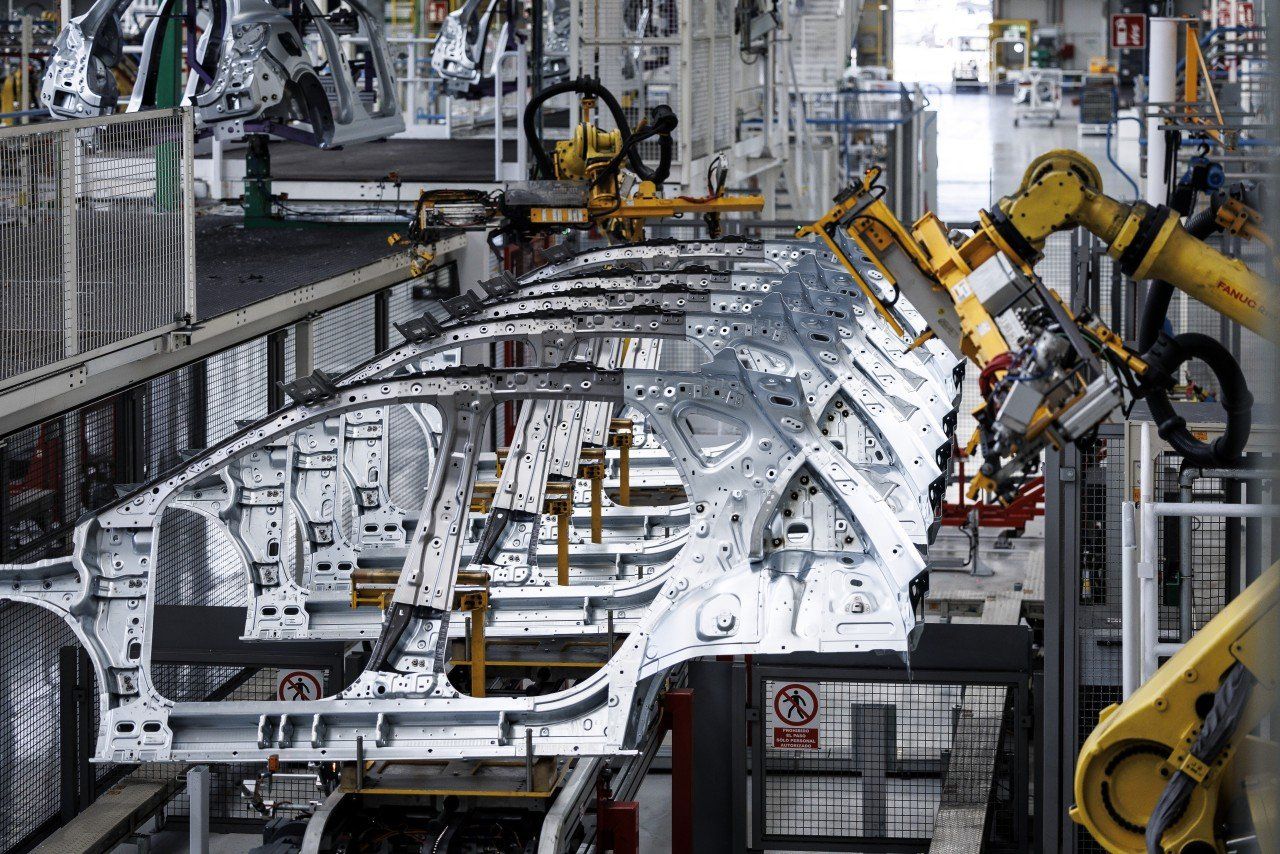
A día de hoy tiene 305.435 m2 construidos y cuenta con 2.259 empleados de los que el 27% son mujeres, una proporción que crece año a año. En 2023 se fabricaron 172.733 vehículos y el 90% de ellos se destina a exportación a 40 países en todo el mundo: Francia (27%), Italia (17%), Reino Unido (9%), Alemania (4%) y Portugal (3%) son los principales destinos fuera de nuestras fronteras. El 23% de la producción acaba fuera de UE.
Así se fabrica un coche tomando como ejemplo la Fábrica de Valladolid de Renault Group:
Taller de Carrocerías
Todo empieza en el departamento de Embutición e Inyección de Plásticos del Taller de Carrocerías (también llamado Taller de Chapa), donde se fabrican las piezas metálicas y plásticas que componen el esqueleto del vehículo. En total se hacen 137 piezas en la Fábrica de Valladolid.
La fabricación de las partes metálicas se inicia en cuatro líneas de corte donde bobinas de acero de hasta 32 toneladas son transformadas en piezas planas. Estas piezas pasan a 13 líneas de embutición. 12 de ellas usan diferentes tecnologías y son de diferentes tamaños para fabricar el techo, el lateral del vehículo, las puertas, refuerzos o traviesas.

Hay una línea más, la línea de embutición en caliente donde las piezas son previamente calentadas en un horno a 900º para mejorar comportamiento mecánico. Después pasan a cinco instalaciones de Corte Láser para recortar o taladrar donde sea necesario. De aquí salen elementos estructurales como refuerzos laterales, refuerzos de piso o largueros.
Los recortes metálicos sobrantes se recogen y transportan automáticamente mediante cintas de transferencia llevando el material a la zona de recuperación de chatarra. Allí se segrega y recicla para su posterior reutilización, un proceso de economía circular que minimiza el impacto ambiental.
En lo referente a las piezas inyectadas en plásticos, se hacen 10 piezas que conforman los paragolpes, embellecedores y portones traseros de Symbioz y Captur. Para este procedimiento el Taller de Inyección de Plásticos cuenta con ocho prensas. Los diferentes tipos de plásticos son transformamos de sólido a líquido mediante calentamiento a temperaturas de en torno a 300 ºC. Se vierten en el interior de cada uno de los 10 moldes y una vez enfriado da lugar a las piezas definitivas. Las piezas plásticas se añadirán más tarde y pasan al Taller de Pintura.

Por su parte las piezas metálicas, antes de darse un baño de color, tienen que pasar por el Taller de Soldadura de la Factoría de Carrocerías. Para hacer una carrocería hay que ensamblar las piezas metálicas anteriormente realizadas y para ello se utilizan 770 robots que manipulan, trasladan y sueldan todas las piezas. Los flujos de piezas se encuentran automatizados mediante 190 AGV (Automatic Guided Vehicles), es decir, vehículos de transporte de movimiento autónomo.
Cada vehículo lleva más de 3.500 puntos de soldadura. Hay cámaras 3D que hacen diferentes medidas para comprobar la soldadura láser del techo y robots que escanean superficie para verificar los cordones de soldadura. También hay cuatro robots con cámaras que son capaces de medir 116 cotas específicas y dimensionales.
Posteriormente se pasa a la línea de ferraje donde se montan las partes móviles de la carrocería, es decir, las puertas y el capó. Los operarios de Renault utilizan pistolas láser al final del proceso para comprobar los juegos y afloramientos de las puertas.

Hay una tercera tarea que se lleva a cabo aquí. El ensamblado de baterías eléctricas de tracción para vehículos híbridos se realiza en el departamento SPB, perteneciente a la Factoría de Carrocerías. Hay dos talleres: uno dedicado al ensamblado de baterías para los híbridos no enchufables (HEV) con una capacidad de 60 baterías a la hora y otro, de reciente creación, dedicado al ensamblado de los híbridos enchufables (PHEV) con una capacidad de 6 baterías a la hora. Una vez ensambladas se llevan al taller de montaje.
Taller de Pintura
Recordemos que tenemos las piezas plásticas por un lado y la caja (carrocería metálica) por otro. Se pintan por separado así que el proceso tiene que ser muy escrupuloso para que la tonalidad coincida exactamente. Por cierto, todas las pinturas son base agua, disminuyendo el impacto medioambiental.

La caja se somete a un baño de cataforesis, un recubrimiento electroquímico que debido a la diferencia de potencial eléctrico hace que las moléculas de pintura se depositen sobre la caja de forma uniforme. Esta primera capa (Base 0) es una protección anticorrosiva. Algunas piezas son huecas y tienen agujeros para que penetre el revestimiento y así esta protección llegue a todas las partes.
Finalizada la cataforesis esos agujeros se tapan con la aplicación de másticos tanto en el exterior como en el interior del vehículo para garantizar la estanqueidad, un proceso del que se encargan 24 robots. Posteriormente toca aplicar una capa base y barniz que da el color final de la carrocería. Hay dos líneas de pintura a la que se añade otra para los vehículos configurados como bitono, en los que el techo lleva un color de contraste. Para estos se hace un proceso de enmascarado y se aplica la capa base y barniz para el techo.
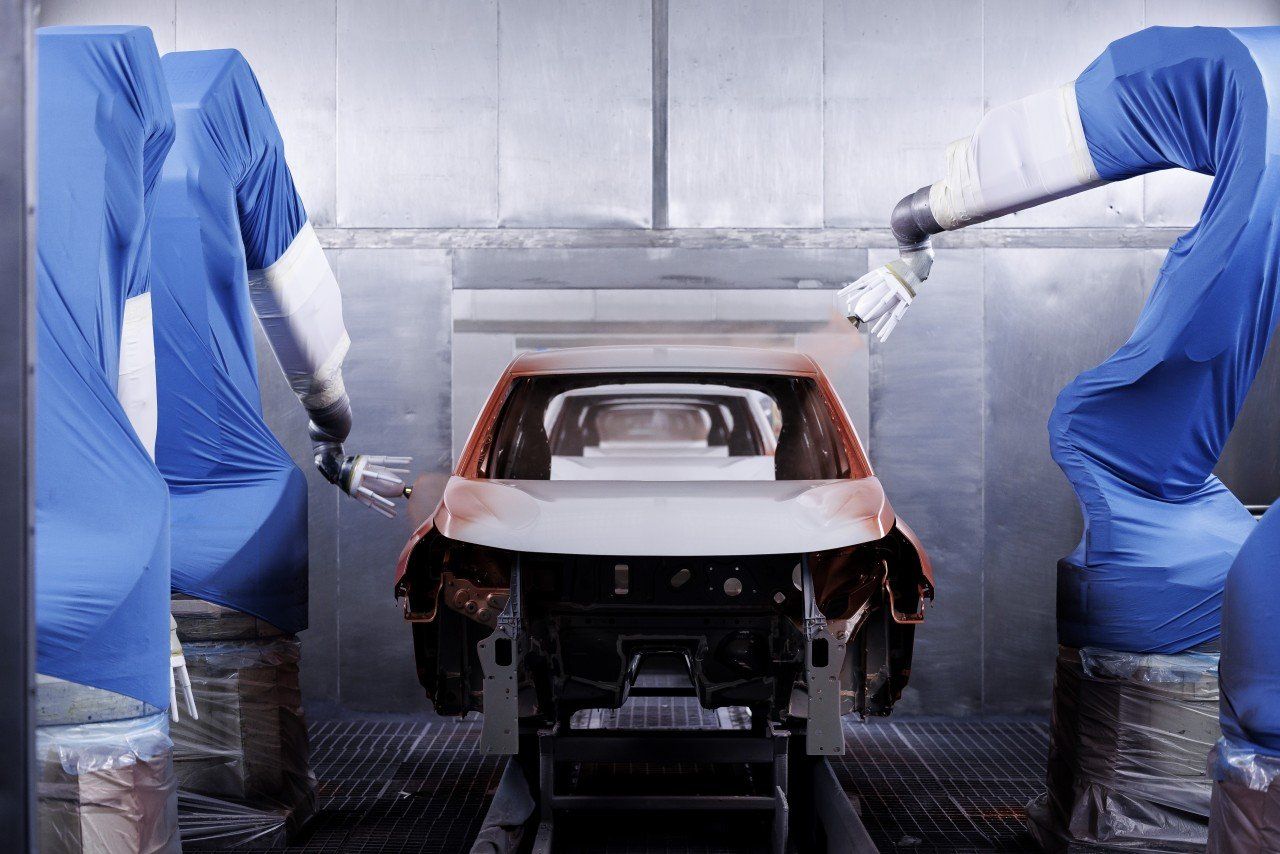
El proceso termina en el túnel de detección automática que controla la calidad. Hay 40 cámaras que realizan 65.000 fotos por vehículo. Sí, has leído bien. La inteligencia artificial se encarga de analizar estas imágenes y avisar a los operarios de zonas que haya que revisar. Así finaliza el viaje de la caja por el departamento de pintura, que es capaz de pintar 900 vehículos al día.
En el Departamento de Pintura de la Factoría de Valladolid destaca la introducción de un nuevo proceso de aplicación de pintura «4WET». Con ello, se aplican las capas una detrás de otra con un único uso del horno al final del proceso. Al no tener que usar el horno tras cada paso se consigue un importante ahorro de energía. El Taller de Pintura ha reducido un 40% del consumo de gas y un 10% el consumo de electricidad en los últimos dos años.

Las piezas plásticas van por otro lado. En el Taller de Pintura, que tiene una capacidad de pintado de 4.800 piezas por día, se pintan los paragolpes delanteros, traseros y el panel del portón. El proceso conlleva la limpieza manual de las piezas para eliminar posibles suciedades, limpieza des ionizante para retirar restos de polvo, flameado de las piezas mediante una llama que asegura la adherencia de la pintura, imprimación, capa de pintura protectora de la superficie, aplicación de color y aplicación de barniz. Por último, hay un proceso de supervisión para comprobar la armonía de color.
Taller de Montaje
La última fase en el proceso de fabricación de estos modelos de Renault es el Taller de Montaje. Es una fase donde la presencia humana es importante y hay 1.121 trabajadores y solo 8 robots. Recordemos que en este punto siguen separadas las piezas plásticas por un lado y la carrocería por otro.
Cuando un vehículo entra en el Taller de Montaje se manda una orden de fabricación al Taller de Montaje Paragolpes con toda la información del paragolpes: color, molduras, diversidad de captadores, etc. Las referencias necesarias para cada paragolpes son preseleccionadas y ubicadas en un carro que, movido por un AGV, acompañará a ese paragolpes en todo el proceso para que el operario no tenga que seleccionar piezas.

El proceso continúa con el punzonado automático para el alojamiento de captadores, soldadura automática mediante ultrasonidos de refuerzos y soportes y se instalan manualmente de todos los componentes. Para finalizar se realiza un test eléctrico y una vez comprobado que todo está en orden del Taller de Montaje Paragolpes se envía a la línea de montaje.
Por un lado está la carrocería pintada, que llega del Departamento de Pintura para que sean montadas todas las referencias en poco más de cuatro horas. Las puertas se quitan para mejorar la ergonomía en las operaciones interiores del vehículo, colocándolas en una balancela sincronizada que las transporta hasta que se vuelven a montar sobre el mismo vehículo.

Sobre la carrocería se montan los tableros (salpicadero, instrumentación, consola, etc) y las piezas plásticas: los paragolpes y el portón trasero. Una vez más todas las referencias necesarias para cada vehículo de la marca del rombo han sido preseleccionadas y ubicadas en una de las 501 mesas transportadoras que acompañará a ese vehículo en todo el proceso.
En otra línea está la pletina del vehículo donde irán los componentes mecánicos. En ella se monta el grupo motopropulsor (motor, transmisión, etc) y el tren de rodaje (suspensión, dirección, frenos, etc). También se añade el tren trasero, el escape y, en el caso de los modelos con hibridación, la batería de alta tensión que viene ensamblada desde la Factoría de Carrocerías.
La pletina y la carrocería se acoplan en un proceso denominado acostaje o boda. El vehículo sigue avanzando por la línea de montaje y se vuelven a instalar las puertas, se ponen las ruedas, se reposta combustible y se añaden otros fluidos necesarios para el funcionamiento. En este punto el coche ya tiene todas sus piezas. El Taller de Montaje de la planta vallisoletana monta 900 vehículos al día.

Tras el montaje, el 100% de los vehículos son sometidos a pruebas en estático y dinámico para comprobar que el funcionamiento es correcto. Se realiza la alineación de las ruedas, el reglaje de haz de luz de faros, el reglaje de la dirección y la calibración de cámaras y radares de los sistemas ADAS. También hay un banco rodaje donde realizan pruebas de aceleración y frenada, en las cuales los vehículos alcanzan los 130 km/h sobre rodillos.
El último paso es la cadena de control de calidad. Renault la llama CSC (Control Satisfacción Cliente) y son controles de una lista de más 100 puntos el vehículo que realizan trabajadores especializados. Revisan la funcionalidad, conformidad y aspecto de cada elemento y el vehículo se prueba en dinámico en una minipista de pruebas. Con esto termina el proceso de fabricación. ¡El coche ya está listo para ser enviado al concesionario!
